What is R-Value? The True Definition
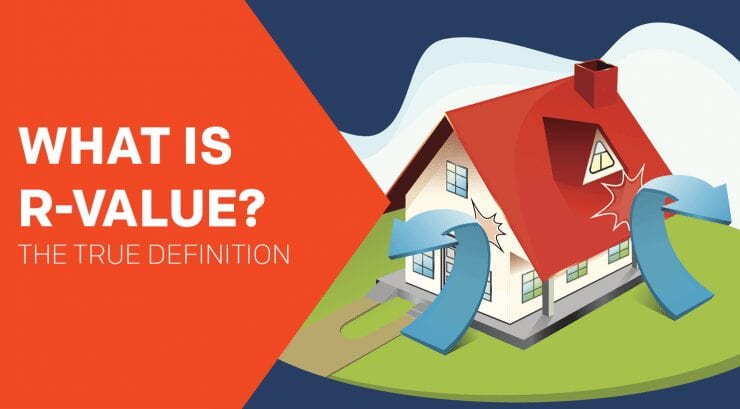
R-value is “the capacity of an insulating material to resist heat flow. The higher the r-value, the greater the insulating power.” (Google Dictionary)
Energy efficiency. Lower utility bills. Comfortable indoor environment. These are all familiar benefits of adding insulation to a home. But how can you tell which products are the best insulators for a particular application?
An “R-value” rating determines the energy saving value of different products.
This article explains how much insulation to use for particular applications.
- How insulation works
- How insulation “r-value” is determined
- Applications and recommendations for insulation
How Insulation Works
According to the second law of thermodynamics, heat always flows towards cold. There are three main ways heat transfers - through conduction, convection, and radiation.
Conduction: The transfer of heat through materials that touch each other, such as a skillet on top of a stove.
Convection: The transfer of heat through liquids and gases. An example of convection is a stove that warms the air around your food.
Radiation: The movement of heat from any source, warming objections around it. One example is the heat emitted from a campfire.
Thermal bridging is the movement of heat across an object that is more conductive than the materials around it.
Most insulation products reduce the conduction of heat flow. An example of this is thermal bridging through wooden studs, which you can learn more about here>
Walls of a home have fiberglass batt insulation in the cavities. But, the wooden studs have a much lower r-value and generally aren’t covered in insulation. The studs create a bridge for heat to travel across. Summer heat moves towards air conditioned spaces indoors. In the winter, heat on the inside moves towards the cold exterior.
Determining R-value
The term "R"-value represents how well insulation restricts heat flow. To test for R-value, a piece of insulation placed between two plates in a laboratory. Heat is then passed through the material to test the thermal conductivity, measured in BTUs per hour. The greater the "R"-value the better the insulation.
The Federal Trade Commission regulates manufacturer claims about insulation. This helps einsure claims are accurate, and not deceiving to consumers. FTC regulations also specify the means by which scientists and manufacturers determine R-value.
Insulated Vinyl Siding R-value Testing
Contoured insulation is not tested for r-value with the standard hot plate method. The ASTM C1363 Standard Test Method, commonly known as the hot box test, is used for these products.
ASTM C1363, better known as the hot box test, place the insulated siding wall assembly between two instrumented chambers. These chambers are called the “climatic chamber” and a “metering chamber.” The chambers are maintained at a specific temperature difference. The climatic chamber is usually cooler than the metering chamber, representing winter conditions. Wind directed at the material simulates true outdoor winter conditions.
During the test, heat flows through insulation from one chamber to another. Scientists measure the amount of energy needed to maintain the temperature in the metering chamber. The R-value of the insulated siding is determined by subtracting the measured R-value of the base wall from that of the entire assembly. This method ensures the claimed R-value represents the "as-installed" performance on the home.
Applications and Recommendations for Insulation
We now know how heat transfers in a home, and how we rate insulation for energy efficiency. Let's look at common products used to insulate parts some parts of a home.
Rigid Foam – Outside walls of homes and below grade. Roughly up to 5.0 per inch.
Spray Foam – Sprayed into the wall cavity, typically in new construction before drywall. Roughly up to 6.5 per inch.
Fiberglass Batt – Rolled into the wall cavity between studs, primarily in new construction. Roughly up to R-3.8 per inch.
Blown In Cellulose – Popular in remodeling projects; holes are cut in the wall to fill the cavity with insulation, or it is sprayed into the attic. Roughly up to R-3.8 per inch.
Foundation and Basement Insulation
Add insulation to a foundation and basement to help save money on utilities to heat the space.
For new construction, add rigid insulation before pouring the foundation. Apply insulation to the exterior walls before adding backfill gravel or dirt.
In remodeling, add insulation to the floor and interior basement walls, then cover with finish materials.
Exterior Walls
In new construction, fiberglass or spray foam insulation is applied between studs. This provides excellent resistance to heat transfer, but leaves a major part of the wall uninsulated.
The wood studs in a home make up 25% of the walls. These studs aren't covered in insulation, creating the perfect opportunity for heat transfer. This is like having one whole wall of the home with zero insulation.
Adding continuous insulation to a home's exterior before siding helps stop energy loss. This can also be done during remodeling applications. The U.S. Department of Energy (DOE) says “when new siding is to be installed, it is a good idea to consider adding insulation under new siding.
Roofs and Attics
Loose-fill or fiberglass insulation added to the floor of the attic helps stop heat from escaping. If you plan to inhabit the attic space, add insulation between the rafters to control the room temperature. Rigid, continuous insulation installed over the rafters helps break the thermal bridge.
Recommendations
The amount of insulation recommended for each application varies depending on the climate zone. To learn more, check out the Energy Star Recommendations for Home Insulation
5 Factors That Influence the Cost of Vinyl Siding
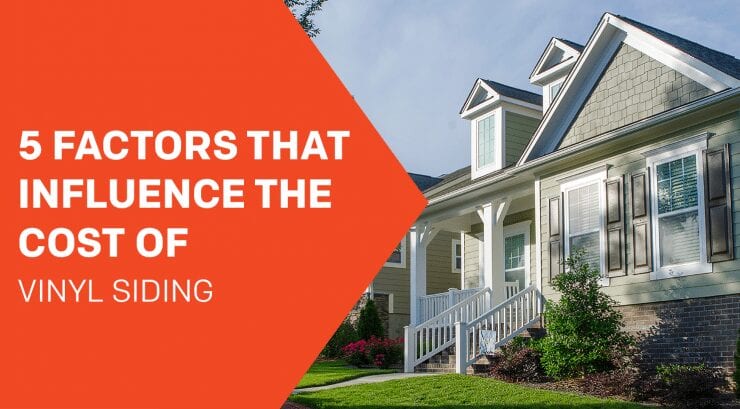
There are a lot of factors that can affect the total cost of new vinyl siding installation. Similar to buying a new vehicle, the cost can vary based on which options you choose. For example, a new SUV with cloth interior may cost around $25,000, while the same vehicle with leather interior may cost $5,000-10,000 more.
In general, vinyl siding costs anywhere from $3.50 - $8.00 per square foot. In this article, we are going to discuss the five main factors that influence the cost of a vinyl siding job:
-
Your home (size, location, design)
-
The condition of current siding and outside walls
-
Product choices
-
Installation process
-
Return on investment
Your Home
Size
Think about the size of your home. Siding materials take up the largest surface area of the outside of a home and are priced by the square foot. The larger the home, the more materials that will be needed, resulting in a higher price.
Location
The location of your home can also impact the cost of your siding job, due to varying labor costs across the country and the cost to ship materials. The price may be more or less depending on what the cost of labor is in your area, and where you are located in relation to the manufacturer or supplier.
Design
How is your home designed? Is it one or two stories? Do you have eaves, gables, or maybe a turret? The design of your home is also a factor when considering the cost of new siding. A taller, two-story home with eaves or gables will require more materials and labor than a one-story ranch or a boxed shaped home. Complex designs with lots of corners and trim work may also require more labor, and generate some extra material waste to complete the installation.
The Condition of your Current Siding
If your current siding needs to be removed prior to the installation of new siding, this can cost an additional $1,000-$3,000. After the old siding is removed, the contractor will inspect the outside walls of the home for any repairs.
If you live in an older home, issues such as rotten wood or termite damage may need to be repaired before the new siding is installed. If the walls of your home are wavy or uneven, your contractor may suggest a flat, rigid insulation added under the new siding to help level out the wall for new siding.
Product Choices
Vinyl siding comes in a wide range of colors and profiles. Premium profiles, accent trim, stone veneer, or other options can increase the overall cost of your project. The thickness of the vinyl siding panel will also have an effect on the cost. Vinyl typically ranges in thickness from 0.04 for more economical options, to 0.05 for premium performance.
When installing vinyl siding, you can choose between insulated and non-insulated. Insulated vinyl siding costs anywhere from $4.00 - $12.00 per square foot installed (compared to non-insulated vinyl at $3.50-$8.00). insulated vinyl siding will generally be more expensive because there is more material in the product. The additional insulation makes it thicker, and therefore more expensive to ship. To learn more about the differences between vinyl siding and insulated vinyl siding read our article here.
Remember that both insulated and non insulated vinyl are completely maintenance free. This means you will not have ongoing maintenance costs such as painting, scraping and caulking as you would with other products, such as James Hardie fiber cement.
Installation Process
Some materials add additional steps to the installation process, resulting in a higher cost for the project. Adding materials like housewrap or rigid insulation are smart decisions for your home, but are not always included in the overall cost.
The time of year can also affect the cost of your project. Having siding installed in off seasons like fall or winter may help you save on labor and materials. Your project may also be completed quicker as your contractor has fewer jobs to install.
If you are installing insulated vinyl siding, the additional thickness can add steps during the installation process. Special accessories and trim work around windows and doors can be required, adding to the cost of the job. Read more on how insulated vinyl siding is installed here.
Return on Investment
According to the 2017 cost vs value report, 76.4% of siding replacement costs are recouped. This is significantly higher than a roof replacement at 68.8%, and a window replacement at 73.9%. As an example, if you spend $20,000 on a siding replacement, you can expect to recoup $15,280, leaving the true cost of your siding around $4,720.
You can also put more money back in your pocket with long-term energy savings. Traditional, non-insulated vinyl siding does not have any true energy saving benefits. With insulated vinyl siding, the average 2-story home without cavity insulation can experience an average savings of 14.2% on heating and cooling costs. Let’s say you’re spending $250 per month on heating and cooling. If your home is similar to the test house, you could be saving $425 per year, every year you are in the home.
Summary
Choosing to reside your home is a major decision. Knowing what is important to you and your family will help guide your decision-making process. To get an accurate estimate, you will need to have a reputable contractor come out to measure and inspect your home. To learn more about how to choose a reliable contractor, download our ultimate guide here.
What is Fiber Cement Siding? Everything you Need to Know
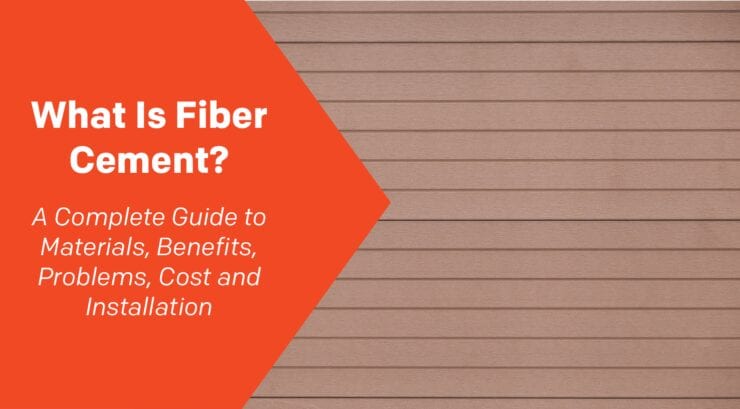
Fiber cement siding, also known as Hardie Board is a siding material that was introduced to the market in the 1980’s as a replacement for asbestos cement siding products. It has become common in some parts of the country, offering design versatility and a solid feel. Some fiber cement siding manufacturers include James Hardie, Nichiha, and Allura.
When researching exterior options for your home, it’s important to understand the benefits, problems, cost and installation of each product. This article will explain what fiber cement siding is made of, what the pros and cons are, how it is installed, how much it costs and some alternative options.
What is Fiber Cement Siding Made Of?
Fiber cement siding is made from a mixture of sand, cement, and cellulose fibers. Asbestos was originally used as the reinforcing material in fiber cement but was replaced with cellulose in the 1980’s due to safety concerns.
What Are the Benefits of Fiber Cement Siding?
Beautiful Appearance
Fiber cement is traditionally available in planks, shingles, and flat boards for vertical applications. It can come pre-painted or pre-stained, and can be painted any color you desire. Fiber cement has an infinite number of color options because it is painted after installation. Fiber cement products are also known for their wood like appearance.
Durability
Most siding products are made to make a home look great, fiber cement can provide a durable exterior solution for your project. Fiber cement is hard to the touch, but because it is heavier and made of a cementitious material it can be prone to cracking and chipping.
What Are The Problems With Fiber Cement Siding?
Maintenance
Products like Hardiplank fiber cement siding will require regular painting to maintain their beautiful appearance, unlike other sidings such as brick or vinyl.
Some factory-painted siding panels are available, and come with up to 15 year warranties that cover peeling, cracking, and chipping. However, many homeowners find themselves needing to repaint their home sooner, and warranties can be very particular about what is covered.
Moisture
Absorptive claddings like fiber cement can hold moisture, leading to panel damage, rot, and even mold problems. It is critical that all installation steps are very carefully followed by a professional to ensure all penetrations and gaps are properly treated with the appropriate paint or caulk to protect the panels from moisture infiltration.
A third party study by Home Innovations Research Labs spanning the course of over a year shows that fiber cement retained less moisture than products like stucco and manufactured stone, but performed worse than brick, vinyl siding, and insulated vinyl siding.
Energy Efficiency
Fiber cement is a cementitious product, therefore it serves as a bridge for energy loss, compared to other more energy-efficient siding products.
According to Table 5-1 of the ASHRAE Fundamentals Handbook, fiber cement has an r-value of .15, better than brick and stone, but lower than vinyl at R-.60, wood at R-.81, and insulated vinyl siding at R-2.0 - 3.5. The American Society of Heating, Refrigerating, and Air-Conditioning Engineers (ASHRAE), is the leading source on design and construction related to heating, cooling, and energy efficiency.
Houses with fiber cement siding can be insulated by adding a layer of energy-saving foam underneath. However, this creates a second step in the install process. Alternative products like insulated vinyl siding add insulation and siding in one step, for an easier, more cost-effective installation. Read more about insulated vinyl siding vs. fiber cement.
How Much Does Fiber Cement Siding Cost?
In general, fiber cement siding costs anywhere from $5.00- $14.50 per square foot installed. The brand of siding, the accessory package, the qualifications of the installer, etc. can all significantly impact the cost of the project.
The cost of fiber cement is comparable to wood, engineered wood, and insulated vinyl siding, but is more expensive than traditional vinyl siding. Read more about the cost of fiber cement here.
How Is Fiber Cement Siding Installed?
The Installation of fiber cement siding can vary depending on the manufacturer. It is extremely important to follow the manufacturer's installation instructions to avoid future issues with the siding panels.
In addition to religiously following installation instructions, installers must also take special steps to protect their health when installing fiber cement. Cutting fiber cement siding generates respirable crystalline silica, a known human carcinogen. Inhaling too much silica can lead to silicosis, lung cancer, and other health problems. Visit www.silica-safe.org for more information. Special saw blades, ventilation, and respirators can be used to limit silica inhalation to a safe level during installation.
Fiber cement can also be brittle before being installed on the wall. Care must be taken to properly store panels, which generally require two people to carry and install. Attention must be paid to the types of nails and guns used to prevent blowouts at the point of fastening on the panel.
This video demonstrates the steps for installing fiber cement siding.
How To Install Fiber Cement Siding (Allura USA)
Alternative Siding Options
Engineered Wood Siding
Engineered wood siding is compressed wood coated with a resin binder to create one solid piece of siding. The siding is embossed with a cedar-grain pattern used to replicate the look of real wood.
These products come in a wide variety of profiles including lap and panel siding. You can choose between pre-primed products and have the home painted after the product is installed, or choose a panel that is pre-painted and ready to install.
Since engineered wood is still considered a wood product, it is susceptible to rot and moisture damage.
Engineered wood products cost around $5.00 – 9.00 per sq.ft. Like Fiber cement, these products require routine maintenance such as painting and caulking, which can add significant cost to the long term price tag.
Insulated Vinyl Siding
Insulated siding is made of a contoured rigid foam backing permanently adhered to vinyl siding. The insulation component of insulated siding is made of expanded polystyrene (EPS) rigid insulation, contoured to perfectly fit the profile of the vinyl siding. The insulation is permanently adhered to the vinyl siding panel during the manufacturing process.
Insulated siding helps reduce heating and cooling costs by wrapping the home in a continuous blanket of insulation, keeping heat inside in the winter and outside in the summer.
The insulation component helps create a great looking exterior by leveling the wall under the siding, reducing imperfections in the wall. The contoured insulation also provides more support to the siding panel, helping it maintain it’s shape and appearance over time and significantly increase durability.
Insulated siding features a perm rating of up to 5.0, allowing your home to breathe and protecting against moisture damage. The foam insulation is also treated with an insecticide that is safe for people and pets but protects the insulation from termite damage.
Insulated Vinyl Siding is maintenance free and requires only periodic cleaning with a garden hose and some soapy water to maintain its original appearance over time.
In general, insulated vinyl siding costs anywhere from $4.00 - $12.00 per square foot installed, although some projects may fall outside this range. Read more about the differences between insulated vinyl siding and fiber cement here.
Final Thoughts
Fiber cement is a common siding product that can improve the appearance of a home, but it also has some disadvantages compared to other products available today. Before investing in new siding, it’s critical to determine which characteristics are important for your particular project.
Can You Paint Vinyl Siding? 5 Factors to Consider
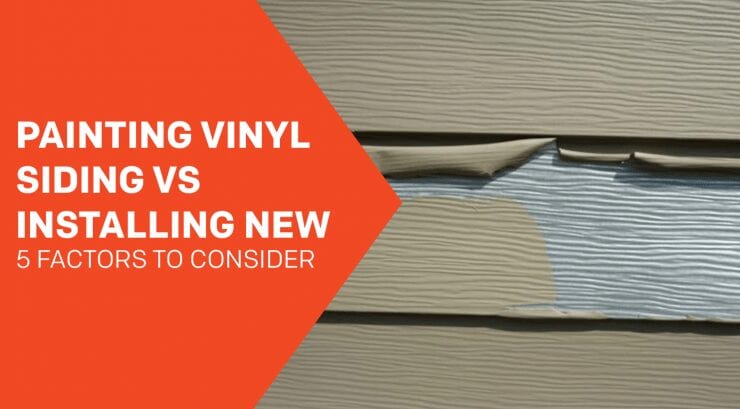
-
Warranty
-
Cost
-
Color
-
Integrity & Durability
-
Insulation
1. Vinyl Siding Warranty
2. Vinyl Siding Cost vs. Painting
3. Integrity of the Siding and the Home
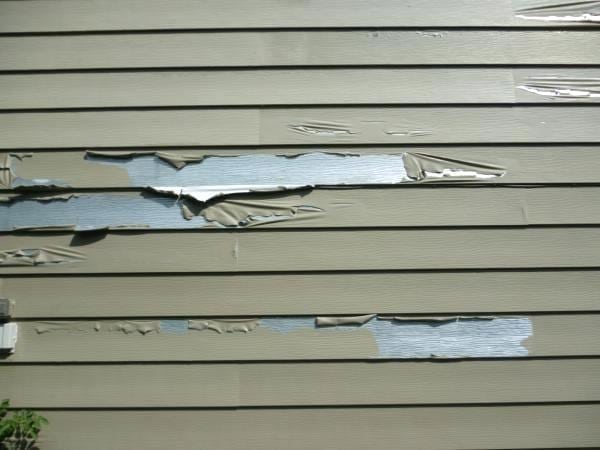
4. Paint Color Selection
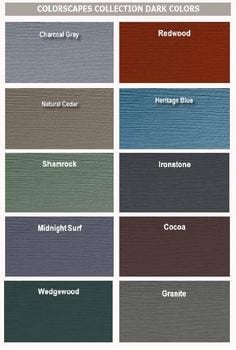
5. Siding and Insulation
Summary
The 5 Biggest Problems with Fiber Cement Siding
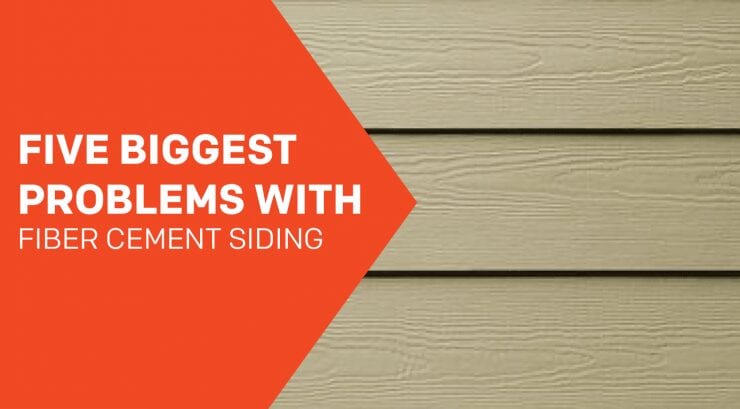
Fiber cement is a siding material that was introduced to the market in the 1980’s as a replacement for asbestos cement siding products. It has become common in some parts of the country, offering design versatility and a solid feel. Some fiber cement manufacturers include James Hardie, Nichiha, and Allura.
With so many siding products available on the market today, it’s important to understand the benefits, as well as the possible problems with James Hardie fiber cement siding. While there are other resources that explain the benefits of fiber cement, this article will explore the five biggest problems with fiber cement siding, including:
Top 5 Problems With Fiber Cement
-
-
Fiber cement siding requires maintenance
-
Fiber cement siding absorbs moisture
-
Fiber cement is difficult to install
-
Fiber cement is not the most environmentally friendly siding
-
Fiber cement is not energy efficient
-
1. Fiber Cement Siding Requires Maintenance
Products like Hardiplank fiber cement siding will require regular painting to maintain their beautiful appearance, unlike other sidings such as brick or insulated vinyl.
Some factory-painted siding panels are available, and come with up to 15 year warranties that cover peeling, cracking, and chipping. However, many homeowners find themselves needing to repaint their home sooner, and warranties can be very particular about what is covered.
Caulking may also be required to help maintain the warranty and protect against the next problem with fiber cement siding we will cover, moisture absorption.
2. Fiber Cement Absorbs Moisture
Absorptive claddings like fiber cement can hold moisture, leading to panel damage, rot, and even mold problems. It is critical that all installation steps are very carefully followed by a professional to ensure all penetrations and gaps are properly treated with the appropriate paint or caulk to protect the panels from moisture infiltration.
Close attention must be paid to all required gap clearances between rooflines and decks during installation, to not put fiber cement in continued contact with more moisture. Any violation of the instructions can create serious moisture concerns and void the product warranty.
A third party study by Home Innovations Research Labs spanning the course of over a year shows that fiber cement retained less moisture than products like stucco and manufactured stone, but performed worse than brick, vinyl siding, and insulated vinyl siding.
3. Fiber Cement is Difficult to Install
In addition to religiously following installation instructions to avoid moisture concerns, installers must also take special steps to protect their health when installing fiber cement. Cutting fiber cement siding generates respirable crystalline silica, a known human carcinogen. Inhaling too much silica can lead to silicosis, lung cancer, and COPD. Visit www.silica-safe.org for more information.
Special saw blades, ventilation, and respirators can be used to limit silica inhalation to a safe level during installation.
Fiber cement can also be brittle before being installed on the wall. Care must be taken to properly store panels, which generally require two people to carry and install. Attention must be paid to the types of nails and guns used to prevent blowouts at the point of fastening on the panel.
4. Fiber Cement is Not the Most Environmentally Friendly
Some people believe that fiber cement is environmentally friendly because it is made from items like cement, fibers, or fly ash. However, the process to produce fiber cement requires the use of a lot of utilities, and the weight of the finished product makes shipping harder on the environment.
A third-party Life Cycle Assessment shows the overall environmental impact of fiber cement to be worse than real cedar siding, stucco, vinyl siding, and insulated vinyl siding, particularly in areas of global warming potential and water intake.
5. Fiber Cement is Not Energy Efficient
Fiber cement is a cementitious product, therefore it serves as a bridge for energy loss, compared to other more energy-efficient siding products.
According to Table 5-1 of the ASHRAE Fundamentals Handbook, fiber cement has an r-value of .15, better than brick and stone, but lower than vinyl at R-.60, wood at R-.81, and insulated vinyl siding at R-2.0 - 3.5. The American Society of Heating, Refrigerating, and Air-Conditioning Engineers (ASHRAE), is the leading source on design and construction related to heating, cooling, and energy efficiency.
Houses with fiber cement siding can be insulated by adding a layer of energy-saving foam underneath. However, this creates a second step in the install process, and sometimes special steps must be taken if the foam is thicker than the siding manufacturer recommendations. Alternative products like insulated vinyl siding add insulation and siding in one step, for an easier, more cost-effective installation. Read more about insulated vinyl siding vs. fiber cement.
Insulated Vinyl Siding vs. Fiber Cement: Which is Best?
Summary
Fiber cement is a common siding product that can improve the appearance of a home, but it also has some disadvantages compared to other products available today. Before investing in new siding, it’s critical to determine which characteristics are important for your particular project.
What is Insulated Vinyl Siding? Materials, Pros, Cons, and Installation
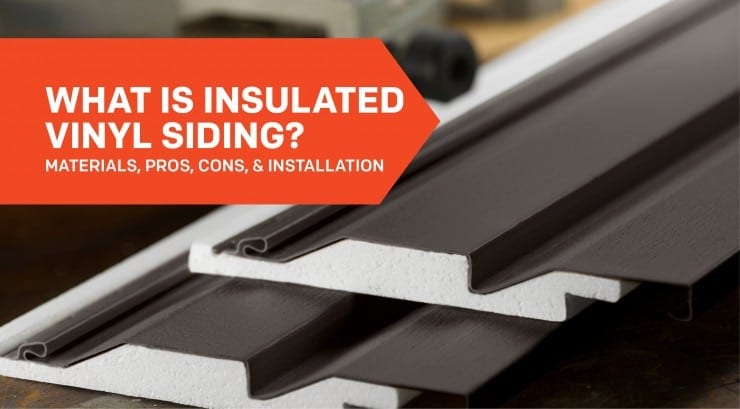
Choosing new siding for your home is a big decision, one that you will likely make only once or twice in a lifetime. There are many types of siding to choose from in the market today, including fiber cement, engineered wood, and insulated vinyl siding, each with their own unique features and benefits.
As the inventors of insulated vinyl siding, we are frequently asked to explain what insulated vinyl siding is, what the benefits and drawbacks are, and how it’s installed.
What is Insulated Vinyl Siding Made Of?
Insulated vinyl siding (also known as foam backed siding) is made of a contoured rigid foam backing permanently adhered to vinyl siding. Vinyl siding made up 39% of the siding market in 2013, making it the most popular siding in America, providing a low maintenance exterior and a wide assortment of design options, including hundreds of colors and various profiles like dutch lap, clapboard, board and batten, shake, and more.
The insulation component of insulated siding is made of expanded polystyrene (EPS) rigid insulation, contoured to perfectly fit the profile of the vinyl siding. The insulation is permanently adhered to the vinyl siding panel during the manufacturing process.
What Are the Benefits of Insulated Vinyl Siding?
Energy Savings
Insulated siding helps reduce heating and cooling costs by wrapping the home in a continuous blanket of insulation, keeping heat inside in the winter and outside in the summer.
Even if you have pink batt insulation between your studs, there may still be an energy leak in your walls. The culprits are the wood studs: heat bypasses the insulation in the wall cavity and transfers through the studs, allowing energy to leak through the walls. This process is called thermal bridging.
Nearly 25% of a home's wall is made of studs that typically aren't insulated, so it's like having one entire wall of the home without insulation.
To combat this problem, the U.S. Department of Energy (DOE) says "when new siding is to be installed, it is a good idea to consider adding insulation under new siding."
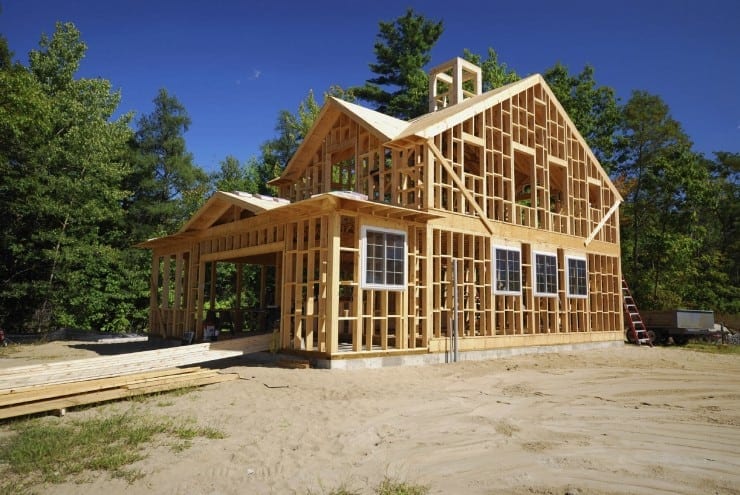
Beautiful Appearance
When you make an investment in new siding, you expect it to look great for a long time to come. Unfortunately, many siding products don’t look as good as they promised, or their appearance degrades over time through exposure to the elements.
The insulation component helps create a great looking exterior by leveling the wall under the siding, reducing imperfections in the wall. The contoured insulation also provides more support to the siding panel, helping it maintain it’s shape and original appearance over time.
Significantly Increased Durability
Most siding products are made to make a home look great, but they aren't designed to provide protection for the house. In fact, traditional vinyl siding products create a hollow void between the back of the siding and the wall, leaving the siding itself susceptible to damage when hit by things like hail, rocks thrown from the lawnmower, or a child's baseball.
Insulated siding provides significantly increased durability compared to traditional vinyl siding. The contoured foam insulation serves as a shock absorber against impact. Insulated siding stands up to the elements, whether they be from mother nature or man made.
Other Benefits of Insulated Vinyl Siding
A More Comfortable Home
By wrapping your home in insulated siding, the inside temperature can be more consistent room to room. The insulation also helps dampen sounds from the exterior, making the interior more quiet.
Termite Protection
The foam insulation is treated with an insecticide that is safe for people and pets, but protects the insulation from termite damage.
Moisture Management
Insulated siding features a perm rating of up to 5.0, allowing your home to breathe and protecting against moisture damage. Despite some misconceptions in the industry that the insulation can contribute to moisture problems, studies completed with the National Association of Homebuilders Research Center proves that insulated vinyl siding actually keeps the wall system drier and more protected than most other siding system available on the market today.
Drawbacks
The primary drawback of insulated vinyl siding is that it’s more expensive than traditional vinyl siding, adding around 20-25% more cost to the job for a homeowner.
Why Does Insulated Vinyl Siding Cost More?
Insulated vinyl siding is considered a more premium product, traditionally made with higher grade vinyl siding that is less susceptible to damage. It is also available in more premium profiles and colors than standard vinyl siding.
The manufacturing process of permanently adhering vinyl to contoured insulation provides more stability to the siding panel, but adds another step in the manufacturing process. It is slightly more expensive to ship to the jobsite, as fewer pieces fit in a box than traditional vinyl siding without insulation due to the additional thickness.
The thickness can also require additional steps during installation. Special accessories and trim work around windows and doors can be required, adding to the cost of the job. Check out our article on the cost of insulated vinyl siding.
How Is Insulated Vinyl Siding Installed?
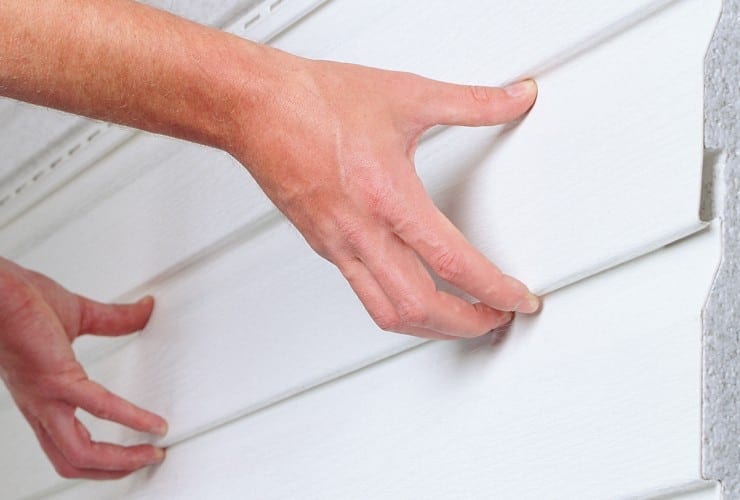
The details of every home are different, and that can impact how insulated vinyl siding is installed. However, there are some basic steps that are standard for most installation projects:
Remove the old siding - This may be required depending on the siding that is currently on the home. Many times insulated vinyl siding can be installed over wood siding if there is no significant damage. Products like old aluminum or vinyl siding are typically removed.
Correct any damage to the wall - Sometimes pre-existing damage is revealed when old siding is removed from a home. If there is any moisture or termite damage, holes in the wood sheathing, etc. this will all need to be corrected before new siding is installed.
Add a weather resistive barrier - Although not required in all situations, it is generally considered a best practice to install a weather resistive barrier such as housewrap before new siding is installed. This helps protect the wall system from water damage.
Install the accessories - Before any siding goes on the wall, it’s important to trim out all windows, doors, and corners. These accessories will create a pocket to receive the insulated vinyl siding for a professional, finished look. A starter strip will also be installed by snapping a level chalk line.
Install the insulated vinyl siding panels - After all the prep work is complete, the wall is now ready for siding. Insulated vinyl siding comes in many profiles; the speed of installation will depend on the particular siding product being used. The bottom of each panel locks into the previous row of siding, and then is attached to the wall through the nailing hem.
Finishing the top of the wall and tight spots - Custom cuts will need to be made of siding is being installed in angled areas, gables, or tight spaces.
Check out our article How to Install Insulated Vinyl Siding in 9 Steps.
Final Thoughts
If you are willing to invest more in your siding project up front, the added benefits of insulated vinyl siding can provide peace of mind, lower utility bills, and a beautiful home for many years.
Fiber Cement Siding Cost: A guide to Pricing, Estimates and ROI
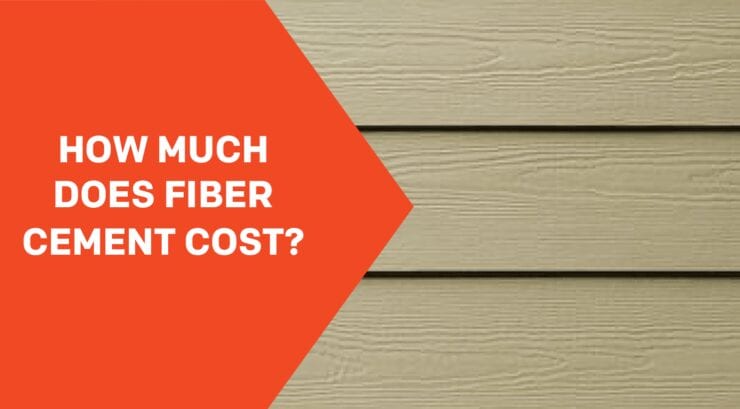
If you’re re-siding your home, the first thing you want to know is how much it will cost, right?
This question is very difficult to answer because every home is different, and there are many options for material, profile, color, and brand on the market today. Buying new siding is similar to buying a number of things, prices can vary drastically based on which options you select.
Things that can impact siding cost:
Location of the home
Size of the home
One, two, or three stories
What siding is currently on the home
Will the old siding need to be removed first
If any previous damage to the home is discovered after the siding is removed
Number of windows, doors, and other openings that must be worked around
Which color or profile you chose
What type of trim is used
Time of year the siding is installed
Adding house wrap or another weather resistive barrier
Additional features to protect against damage from moisture or pests
Energy savings rating (r-value) of the insulation you chose
Qualifications of the installation company - licensed, bonded, insured?
General Pricing Guidelines for Fiber Cement
In general, fiber cement siding costs anywhere from $5.00- $13.50 per square foot installed. The brand of siding, the accessory package, the qualifications of the installer, etc. can all significantly impact the cost of the project.
The cost of fiber cement is comparable to wood, engineered wood, and insulated vinyl siding, but is more expensive than traditional vinyl siding.
Fiber cement siding is made from a mixture of sand, cement, and cellulose fibers. It is traditionally available in planks, shingles, and flat boards for vertical applications. It can come pre-painted or pre-stained and can be painted any color you desire.
Fiber cement offers minimal energy savings at .15 r-value but can be installed with fanfold or insulating sheathing products to improve the r-value of the whole siding system.
Fiber cement is hard to the touch, but because it is heavier and made of cementitious material, it can be prone to cracking and chipping. It is also considered an absorptive cladding, meaning it can absorb moisture, which can lead to problems such as rot.
Return on Investment for Fiber Cement
The Cost vs. Value report, published by Remodeling Magazine, provides an estimate of how much cost from home improvement projects will be recouped by adding value to the home.
The 2019 report shows that a siding replacement recoups 75.6% of the cost, significantly better than a bathroom addition (58.1%), a major kitchen remodel (59.7%), roof replacement (68.2%), or even replacing windows (70.8%).
Keep in mind these costs do not include routine maintenance. Fiber cement requires regular caulking and repainting to protect the siding. Paint can cost anywhere from $1.5-3/sq.ft. which is about $3,000-$6,000 every time it’s done.
How Much Siding Will Your Project Require?
Knowing the estimated cost of siding per square foot is good, but it’s not very useful unless you know how much siding your home will require. Below are some general guidelines to determine the amount of siding you will need.
Because every home is different, we recommend always contacting a qualified professional to get accurate measurements.
Square and Rectangular Walls
Height x width = total per wall
Do not subtract any entry doors or windows, unless it’s a large picture window.
You will subtract the area of the garage door if you have one.
Gables
Height x width x .75 = total per gable
If a gable is hard to reach, a quick trick is to measure the height of the current siding profile, then multiply by the number of courses on that wall section.
Dormers
Height x width x 1.5 = total per dormer (this gives you enough material for both sides)
Add up the area from all walls to give yourself a rough idea of how many square feet of siding your home will require. Check out this short video for more detail about measuring for siding.
Examples
The average home requires 1500 - 2500 square feet of siding material.
1,000 square feet of siding = $5,000 - $13,050
1,500 square feet of siding = $7,500 - $20,250
2,000 square feet of siding = $10,000 - $27,000
2,500 square feet of siding = $12,050 - $33,750
Other Siding Options
Engineered Wood Siding
Engineered wood siding is compressed wood coated with a resin binder to create one solid piece of siding. The siding is embossed with a cedar-grain pattern used to replicate the look of real wood.
These products come in a wide variety of profiles including lap and panel siding. You can choose between pre-primed products and have the home painted after the product is installed, or choose a panel that is pre-painted and ready to install.
Since engineered wood is still considered a wood product, it is susceptible to rot and moisture damage.
Engineered wood products cost around $5.00 – 9.00 per sq.ft. Like Fiber cement, these products require routine maintenance such as painting and caulking, which can add significant cost to the long term price tag.
Insulated Vinyl Siding
Insulated siding is made of a contoured rigid foam backing permanently adhered to vinyl siding. The insulation component of insulated siding is made of expanded polystyrene (EPS) rigid insulation, contoured to perfectly fit the profile of the vinyl siding. The insulation is permanently adhered to the vinyl siding panel during the manufacturing process.
Insulated siding helps reduce heating and cooling costs by wrapping the home in a continuous blanket of insulation, keeping heat inside in the winter and outside in the summer.
The insulation component helps create a great looking exterior by leveling the wall under the siding, reducing imperfections in the wall. The contoured insulation also provides more support to the siding panel, helping it maintain it’s shape and appearance over time and significantly increase durability.
Insulated siding features a perm rating of up to 5.0, allowing your home to breathe and protecting against moisture damage. The foam insulation is also treated with an insecticide that is safe for people and pets but protects the insulation from termite damage.
Insulated Vinyl Siding is maintenance free and requires only periodic cleaning with a garden hose and some soapy water to maintain its original appearance over time.
In general, insulated vinyl siding costs anywhere from $4.00 - $12.00 per square foot installed, although some projects may fall outside this range. Read more about the differences between insulated vinyl siding and fiber cement here.
Final Thoughts
There are many factors that can affect the cost of your siding, no matter what product you chose. To get an accurate cost, it’s critical that you contact a qualified contractor who can show you the best options for your home and provide an accurate price.
Do your research before selecting a contractor. There are many websites available today where you can check what other consumers are saying about local contractors. For instance, Angie’s List, Service Magic, Yelp and the Yellow Pages are good resources to gather recommendations or complaints. You can also request references from the contractor directly. Learn more about how to choose a contractor here
5 Problems with Insulated Vinyl Siding: True or False?
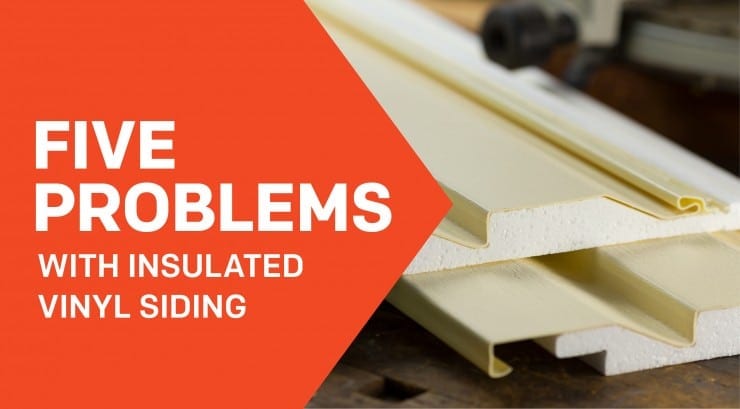
5 Problems with Insulated Vinyl Siding: True or False?
Every home siding product on the market today has features, benefits, and downsides. Finding the siding that is right for your project requires some research to see how each product aligns with your specific needs. This article discusses 5 problems with insulated vinyl siding (also known as foam backed siding) and if they are true or false.
Is maintenance freedom important to you, or do you want the ability to change the color of the siding from time to time by painting? Are you comfortable investing in the siding you truly want because you plan to stay in your home for years, or are you moving soon and want an affordable enhancement to curb appeal?
Whatever your situation, there will be plenty of myths and facts to sort through about each siding product available to you. As the inventors of insulated siding, we wanted to address a few of the common questions we receive related to the product. Below is our list of five problems associated with insulated vinyl siding, and if they are true or false.
1.) Is Insulated Vinyl Siding Harder to Install?
The short answer is yes, installing insulated vinyl siding requires a few additional steps than traditional vinyl siding. Although installing insulated vinyl siding is not a far departure for those that are experienced vinyl siding installers, the additional thickness of the foam insulation requires a few changes.
For starters, you will require a few additional tools. Hollow vinyl siding can be cut with only a pair of hand snips, but insulated vinyl siding will require a table or hand saw. Use a fine tooth blade installed backwards in the saw, or use a siding specific blade.
Aside from cutting the siding panels, insulated vinyl siding will require more build out around windows, doors, and other openings. This is due to the additional thickness of the insulation, which makes the siding project farther out from the wall. Be sure to use accessories with wider receiving pockets to accept the full thickness of the insulation.
When it comes to getting the product to the job site, more boxes, or larger boxes, are required for insulated vinyl siding. Because of the additional thickness of the foam, not as many pieces can fit in a standard box.
Conclusion: Yes insulated vinyl siding is harder to install than traditional vinyl siding panels.
2.) Is Insulated Vinyl Siding More Expensive Than Vinyl?
Prices on siding products can vary substantially based on what features and benefits are selected. Just like buying a vehicle, if you get a lower grade car but add all the bells and whistles, it may end up costing the same or more than an entry level model of a higher end car.
However, in general insulated vinyl siding is more expensive than hollow vinyl siding. Read more about the cost of insulated vinyl siding here. This is due to the energy saving blanket of insulation adhered to the back of every siding panel. When new siding is installed, it is recommended by the Department of Energy that you add insulation. Insulated vinyl siding is a great way to improve the appearance of your home with new siding while adding insulation that will help reduce your utility bills, all in one step.
The foam board not only helps insulate the home, but also provides additional stability and durability to the siding panel. This allows vinyl siding manufacturers to make insulated siding in wider, flatter profiles and richer, darker colors than before. These premium profiles and colors can add some cost to your siding project.
Finally, insulated vinyl siding is thicker than traditional siding due to the foam insulation, which requires some additional steps or special accessories that can increase the installed cost.
Conclusion: Yes, insulated vinyl siding is more expensive than traditional vinyl siding.
3.) Does Insulated Vinyl Siding Create Moisture Problems?
There are two primary source of potential moisture damage in a wall: water vapor generated inside the home that needs to escape to the outside, and bulk water from the outside that infiltrates the siding system, such as driving rain. Let’s start by addressing water vapor.
Handling Water Vapor from the Inside
Did you know that the average family of four generates four to six gallons of water vapor inside every day? The water vapor is generated through activities such as cooking, cleaning, bathing, and even just breathing!
When adding products to the outside of a house, particularly a slightly older home that doesn’t have a new HVAC system that handles moisture build up, it’s important to make sure you aren’t trapping any water vapor inside the home. When adding insulation in particular, the goal is to tighten up the home to reduce energy loss, but the wrong products can also prevent water vapor from escaping.
The way to gauge a product’s ability to let water vapor escape and let a home breath is the perm rating. The insulating foam used in insulated vinyl siding features a perm rating of up to 5.0, providing much better breathability tha comparable insulation products with perm ratings of 1.5 or less. Because of this breathability, installing insulated vinyl siding does not require costly venting as do some other insulation materials.
Therefore, insulated vinyl siding does not create moisture problems from water vapor generated inside the home. But what about bulk water from the outside?
Handling Bulk Water from the Outside
According to an article from FineHomebuilding.com, “Controlling rain is the single most important factor in the design and construction of durable buildings and in the control of mold. It doesn’t matter what your house is clad with, your siding leaks. Water always finds a way behind siding.”
If it’s guaranteed that the exterior of the home is going to be infiltrated by rain and other sources of moisture, then it’s important to select products that allow the wall to dry out quickly to help prevent mold or mildew damage.
Because insulated vinyl siding contains a rigid foam core, some people have thought the foam might absorb and mold moisture. However, a one year study completed by the Senior Energy Engineer at the Home Innovations Research Labs (HIRL) proved that insulated vinyl siding does not create moisture problem. In fact, of nine different wall assembly types such as hollow vinyl siding, manufactured stone, fiber cement, and brick, insulated vinyl siding kept the wall dryer than any other cladding option.
You might wonder how that can be, considering other claddings create a leakier system overall. According to Craig Drumheller, Senior Energy Engineer, “Insulated siding provides both thermal and hygrothermal benefits in light framed wall construction. The thermal resistance of insulated siding provides a double benefit: reduced heat flow in the wall assembly, thereby saving energy, and a higher wall cavity temperature, resulting in increased drying capacity.”
In simple terms, because insulated vinyl siding keeps the wall warmer due to it’s energy saving properties, it also helps the wall dry out faster.
Conclusion: No, insulated vinyl siding does NOT cause moisture problems.
Click here to learn more about the year long moisture study >
Click here for more testing related to the moisture management of insulated siding >
4.) Does the Foam and Insulation Separate Over Time?
Insulated vinyl siding is made of two primary components: rigid foam insulation and vinyl siding. The vinyl siding acts as a skin, permanently adhered to the insulating foam core. The adhesive used to attach the siding to the vinyl actually cures to create a permanent bond between the two components. Learn more about this process in the video below.
Conclusion: No, the foam and vinyl will not separate over time.
5.) Is Insulated Vinyl Siding New and Untested?
Although you may have only heard of insulated vinyl siding recently, it is a product that has been around for many years The first insulated vinyl siding product was launched in 1996 as a collaboration between Progressive Foam and Crane Performance Siding. Since that time, every major vinyl siding manufacturer has launched their own versions of insulated vinyl siding, and between these groups it has been installed on over half a million homes.
You can rest easy knowing that hundreds of thousands of people have put insulated vinyl siding on their homes. With robust warranties of 25+ years, all the way up to double lifetime, we are confident that even the earliest installed products are still standing up to the test of time.
On top of a great track record, insulated vinyl siding is backed by a mountain of third party certified testing data. Everything from moisture management, energy efficiency, environmental impact, and more have been thoroughly tested over the years. You can have confidence that you are selecting very well vetted products to help protect and improve the appearance of your siding.
Conclusion: No, insulated vinyl siding is not new; it has been around for over 20 years.
Click here more technical information on insulated vinyl siding >
Other Related Topics
Insulated Vinyl Siding Cost: A Guide to Pricing, Estimates, and ROI
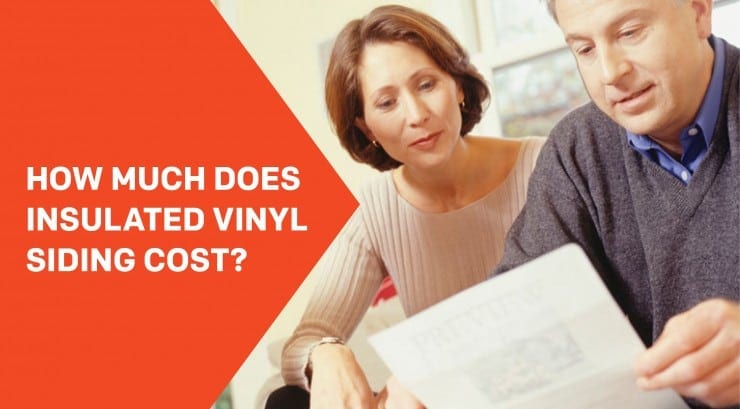
One of the most common questions we receive from homeowners that are shopping for new siding is: How much does insulated vinyl siding cost?
This question is very difficult to answer because every home is different, and there are many options for material, profile, color, and brand on the market today. Buying new siding is similar to buying a vehicle; prices can vary drastically based on which options you select.
Do you need a car, van, or truck? Do you prefer all-wheel drive, power windows, leather or cloth interior?
How about a sunroof, chrome finishes, a backup camera or GPS? Do you prefer a two-door or four-door, maximum gas mileage or more towing capacity?
If you’re commuting an hour each direction every day or using your vehicle as a work tool to get the job done, your needs may be drastically different.
Things that can impact insulated vinyl siding cost are:
- Location of the home
- Size of the home
- One, two, or three stories
- What siding is currently on the home
- Will the old siding need to be removed first
- If any previous damage to the home is discovered after siding is removed
- Number of windows, doors, and other openings that must be worked around
- Standard or premium profiles be used, such as shake, board and batten, etc.
- Lighter shades or premium, darker colors
- Accent trim package selected
- Time of year the siding is installed
- Adding housewrap or another weather resistive barrier
- Additional features to protect against damage from moisture or pests
- Energy savings rating (r-value) of the insulation
- Qualifications of the installation company - licensed, bonded, insured?
General Pricing Guidelines for Insulated Vinyl Siding
In general, insulated vinyl siding (also known as foam backed siding) costs anywhere from $4.00 - $12.00 per square foot installed, although some projects may fall outside this range. The grade of siding, the accessory package, the qualifications of the installer, etc. can all significantly impact the cost of the project. Insulated vinyl siding is typically more expensive than traditional non-insulated siding, but comes with valuable benefits. To learn more about the benefits of insulated vinyl siding, check out What is Insulated Siding: Materials, Pros, Cons, and Installation>
Insulated vinyl siding is typically made with high grade vinyl siding to better protect it from damage, fading, or warping. It is also available in more premium profiles such as double 6” or single 7” and darker, richer colors than traditional vinyl.
During the manufacturing of insulated siding, the contoured foam insulation is permanently adhered to vinyl siding, giving it more stability but adding a step in the process. To see this process in action check out this video on Making Insulated Vinyl Siding.
Due to the added thickness of the foam, fewer pieces can fit in a box than traditional siding, making it slightly more expensive to ship to a job.
The thickness can also require additional steps during installation. Special accessories and trim work around windows and doors can be required, adding to the cost of the job.
Return on Investment for Insulated Vinyl Siding
The Cost vs. Value report, published by Remodeling Magazine, provides an estimate of how much cost from home improvement projects will be recouped by adding value to the home.
The 2017 report shows that a siding replacement recoups 76.4% of the cost, significantly better than a bathroom addition (53.9%), major kitchen remodel (65.3%), roof replacement (68.8%), or even replacing windows (73.9%).
Therefore, if your new siding cost $20,000, you could expect to recoup $15,280 dollars in added value to your home, leaving the true cost at $4,720.
Insulated vinyl siding will also reduce the heating and cooling costs for your home, helping to pay back the original cost over time.
Financing Options
Another benefit of working with a professional contractor to install insulated vinyl siding is that many offering financing options, some with zero or low-interest rates, to help spread out the cost of new siding.
With some standard options available to insulated vinyl siding contractors such as Greensky Financing, a $20,000 siding job can be financed for as low as $250/mo. For 120 months.
This way you can hold onto your money longer and spread out the expensive of a new siding job over a longer period of time.
How Much Siding Will Your Project Require?
Knowing the estimated cost of siding per square foot is good, but it’s not very useful unless you know how much siding your home will require. Below are some general guidelines to determine the amount of siding you will need.
Because every home is different, we recommend always contacting a qualified professional to get accurate measurements.
Square and Rectangular Walls
Height x width = total per wall
Do not subtract any entry doors or windows, unless it’s a large picture window.
You will subtract the area of the garage door if you have one.
Gables
Height x width x .75 = total per gable
If a gable is hard to reach, a quick trick is to measure the height of the current siding profile, then multiply by the number of courses on that wall section.
Dormers
Height x width x 1.5 = total per dormer (this gives you enough material for both sides)
Add up the area from all walls to give yourself a rough idea of how many square feet of siding your home will require. Check out this short video for more detail about measuring for siding>
Examples
The average home requires 1500 - 2500 square feet of siding material.
1,000 square feet of siding = $4,000 - $12,000
1,500 square feet of siding = $6,000 - $18,000
2,000 square feet of siding = $8,000 - $24,000
2,500 square feet of siding = $10,00 - $30,000
Other Important Terminology
When gathering quotes, you may hear some other terminology related to the installation of new siding. A few of those are listed below, although there may be more accessories required for your specific project
Squares
Siding is typically ordered in “squares.” One square of siding is simply 100 square feet of material. Therefore, if you estimate the exterior of the home is 2,000 square feet, it would require 20 squares of siding.
J-channel
A popular accessory piece used to trim out windows, doors, and other openings on the wall. J-channel provides a pocket for the insulated vinyl siding to slide into for a finished look.
Corner posts
Installed at the all exterior corners of the house, corner posts also feature a pocket for the siding panel to slide into. Corner posts can be a little difficult for novice installers to install perfectly, so we recommend always using an insulated corner post insert - these snap in to the vinyl corner post to provide rigidity and protection from impact damage, and also complete the blanket of insulation around the home.
Inside posts
Inside corner posts are used anywhere two corners come together to form an inverted 90 degree angle, such as under a porch covering. These posts provide a clean pocket for the siding to slide into.
Starter Strips
Insulated vinyl siding panels lock together as they are installed up the wall, but the first panel requires a starter strip to kick things off. Contractors will snap a chalk line to ensure the starter strip is straight, then the first panel of siding will be locked in before being nailed to the wall.
Aluminum coil
Many times contractors will use aluminum coil and a break to fashion custom flashing and coverings from trim and other parts of the installation. For insulated vinyl siding, the trim pieces must sometimes be built out to accommodate for the additional thickness of the foam. A skilled contractor will use aluminum coil to cover the built out trim for a clean, finished look. Check out this video about capping with aluminum coil>
Final Thoughts
To get an accurate cost of insulated vinyl siding for your project, it’s critical that you contact a qualified professional who can show you the best options for your particular home.
Be wary of contractors who present you with an insanely low price - they may be cutting corners or leaving out critical components that could cost you more money once the job is done.
Other Related Topics
Insulated Vinyl Siding vs. Fiber Cement: Which is Best?
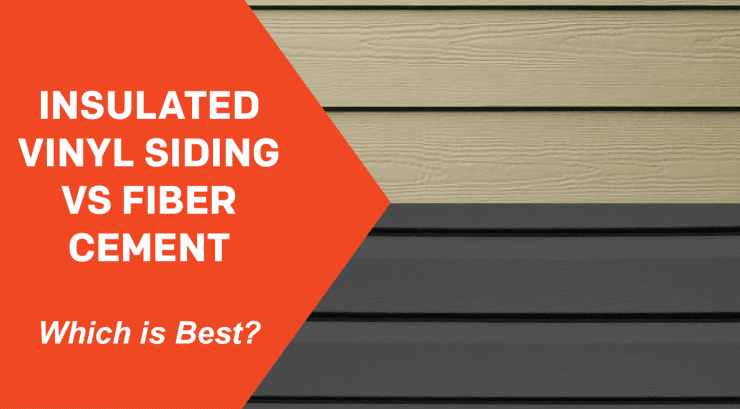
Insulated Vinyl Siding vs. Fiber Cement
There are many siding products available on the market today to give the exterior of your home a beautiful appearance and protect it from the elements, but two products that are gaining popularity are insulated vinyl siding and fiber cement siding. In this article we will take a look at Insulated Vinyl Siding vs. Fiber Cement to help you determine which may be right for your project.
Composition
Insulated vinyl siding is made of rigid, contoured insulation permanently adhered to vinyl siding, while fiber cement siding is made from a mixture of sand, cement, and cellulose fibers. A third party Life Cycle Assessment found that insulated vinyl siding has a lower overall environmental impact than fiber cement, second only to traditional vinyl siding and cedar.
Appearance
Both insulated vinyl siding and fiber cement are designed to replicate the look of traditional wood siding planks. Both products can effectively cover exterior walls to improve the appearance of the home.
Insulated Vinyl Siding
Insulated vinyl siding provides a wider selection of design options that fiber cement. Clapboard, dutchlap, board and batten, shakes, scallops, and even panels designed to look like cabin logs are all available, in addition to extensive accessories to complete the look of the home.
Insulated vinyl siding typically features a significant butt height that creates deep shadow lines to emulate the look of real wood.
Fiber Cement
Fiber cement is traditionally available in planks, shingles, and flat boards for vertical applications. It can come pre-painted or pre-stained, and can be painted any color you desire. Although insulated vinyl siding is available in hundreds of colors, fiber cement has an infinite number of color options because it is painted after installation.
Energy Efficiency
The energy efficiency of insulation products is measured in R-value, which means the resistance to heat flow. The higher the r-value, the greater the insulating power. Tiny air pockets in the insulation resist the transfer of heat. The thicker the insulation, the more air pockets, and the higher the r-value.
Insulated Vinyl Siding
Depending on the particular brand and product, insulated vinyl siding features an r-value of 2.0 - 3.5. The thick insulation component helps reduce energy use and lower utility bills. For more information about how much insulated vinyl siding can save, check out this article about cost and return on investment.
Fiber Cement
Fiber cement offers minimal energy savings at .15 r-value, but can be installed with fanfold or insulating sheathing products to improve the r-value of the whole siding system.
Durability
Fiber Cement
Insulated vinyl siding and fiber cement can both provide a durable exterior solution for your project. Fiber cement is hard to the touch, but because it is heavier and made of a cementitious material, it can be prone to cracking and chipping. It is also considered an absorptive cladding, meaning it it can absorb moisture, which can lead to problems such as rot.
Insulated Vinyl Siding
Insulated vinyl siding is made with a tough plastic material that is impervious to water damage, cracking and chipping. Although traditional vinyl siding is susceptible to impact damage because of the hollow void created between the siding and the wall, insulated vinyl siding provides superior impact resistance. The contoured foam insulation serves as a shock absorber for the siding, protecting it from damage due to hail, rocks thrown from the lawnmower, or the neighbor’s baseball. Check out the video below where an ice ball is shot at insulated vinyl siding.
Maintenance
Fiber Cement
Of the two siding products, insulated vinyl siding requires the lowest maintenance by far. Fiber cement requires regular caulking and repainting to protect the siding from the elements and maintain a beautiful appearance, which can be costly and time consuming.
Insulated Vinyl Siding
Insulated vinyl siding requires only periodic cleaning with a garden hose and some soapy water to maintain its original appearance over time.
Cost
Insulated Vinyl Siding
Depending on your area of the country, which options you select, and the design of your home, prices for fiber cement and insulated vinyl siding can fluctuate greatly. In general, insulated vinyl siding costs anywhere from $4.00 - $12.00 per square foot installed.
Fiber Cement
The 2015 Remodeling Magazine Cost vs. Value Report listed the average price for 12.5 squares of fiber cement siding installed as $14,014 and foam-backed vinyl siding at $15,184. However, it is important to remember that insulated vinyl siding does not require expensive, routine maintenance such as painting and caulking, which can cost up to $6,000 each time per Home Advisor.
In addition, the energy efficiency of insulated vinyl siding can reduce your utility bills every single year it is on your home, significantly reducing the true cost of the project over time.
Installation
Fiber Cement
Fiber cement siding is durable and solid once it is installed on the wall, but it can be delicate during handling in shipping and on the jobsite. Fiber cement installation requires two people to handle all panels to prevent breakage, while insulated vinyl siding can be installed with one person.
Popular brands of fiber cement also kick off silica dust when they are cut. Excessive exposure to silica dust can result in a potentially fatal lung disease, so it is recommended that installers use a respirator when cutting the panels. In comparison, insulated vinyl siding can be cut with snips or a circular saw, and does not require any special safety equipment.
The video below shows a side by side installation comparison for both products.
VSI HardiePlank vs. Vinyl Siding video (Fernando)
Warranty
Insulated Vinyl Siding
The warranty for your project will depend on the particular brand and profile of siding you select. In general, many insulated vinyl siding manufacturers offer warranties of 30, 40, 50 years or more. As the inventors of insulated vinyl siding and the manufacturer of the foam component, we offer a transferable lifetime warranty in addition to the warranty from the vinyl manufacturer, providing double coverage.
Fiber Cement
Many fiber cement manufacturers also offer a 30 year warranty, with coverage specific to the product selected and the geography of the install.
Summary
Both fiber cement and insulated vinyl siding can help you achieve a beautiful exterior for your home. In general, insulated vinyl siding is going to perform better in the categories of energy savings, long term durability, and low maintenance. Fiber cement can create a completely unique look because it can be painted any color you want, but will require routine maintenance to upkeep that appearance over time.
It’s important to take the special circumstances of your project into consideration when deciding between fiber cement and insulated vinyl siding.
Insulated Vinyl Siding |
Fiber Cement Siding |
|
Appearance |
✓ |
✓ |
Energy Savings |
✓ |
|
Durability |
✓ |
|
Maintenance |
✓ |
|
Cost |
✓ |
✓ |
Installation |
✓ |
|
Warranty |
✓ |
Other Related Topics